Der Zementanlagenbau ist ein herausfordernder und sehr anspruchsvoller Prozess. Dies ist im Wesentlichen auf vier einschränkende Parameter zurückzuführen: die geringen Stückzahlen, die sehr großen Abmessungen der Anlagen, die Notwendigkeit einer extrem hohen Anlagenverfügbarkeit und die Anforderungen, die sich von Auftrag zu Auftrag ändern (z. B. Anlagengröße, Lieferumfang, Verfahrenstechnik, Logistikkonzept usw.). Infolgedessen sind viele, wenn nicht die meisten Projekte aus technischer Sicht einzigartig.
3D Modell eines Kühlergehäuses. Um die Komplexität der Automation zu reduzieren, wurde die Konstruktion in separate Module aufgeteilt.
Dieser neue Ansatz ermöglicht maßgeschneiderte Lösungen nach den Wünschen unserer Kunden - ohne unseren Engineering-Aufwand drastisch zu erhöhen. Und unsere hohe Produktqualität wird noch weiter gesteigert.
Dr. Justin Bisping
Leiter der Business Unit Design and Engineering Pyroprocessing
Technologies, thyssenkrupp Industrial Solutions
Neben den meist einmaligen Parametern unterliegen Projekte im Anlagenbau der allgemein gültigen Forderung nach schnellen und kostengünstigen Lösungen auf Basis hochwertiger und sicherer Produkte. Diese Herausforderungen haben in den letzten Jahrzehnten zu einem Kompetenzaufbau bei namhaften Anbietern und dem Einsatz der Finite-Elemente-Methode (FEM) zur rechnerischen Optimierung geführt. Bisher beschränkte sich dieser Ansatz jedoch typischerweise auf die individuelle Projektentwicklung oder Produktpflege, während eine spontane Integration in ein laufendes Projekt aufgrund begrenzter Verarbeitungs- oder Programmierkapazitäten nur selten möglich war.
Diese Schwierigkeiten waren Ausgangspunkt und Motivation für einen neuen Ansatz, den Spezialisten der Business Unit Cement Technology bei thyssenkrupp Industrial Solutions entwickelt haben und der auf modernsten Engineering-Tools - 3D-CAD in Kombination mit FEM - und hochautomatisierten Standardaufgaben, wie z. B. der Erstellung von Fertigungszeichnungen, basiert. Dadurch können nun im Rahmen eines laufenden Vertrages Optimierungen im laufenden Projekt und auftragsspezifische Anpassungen vorgenommen werden.
Beispielhafte Darstellung einer rechnerischen Optimierung einer Sohlplatte eines Drehrohrofens. Eine Topologieoptimierung diente als Grundlage zur Gewichts- und Fertigungsoptimierung.
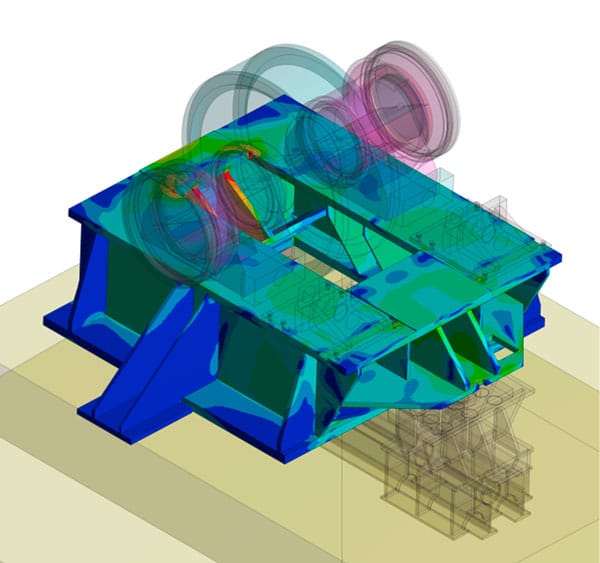
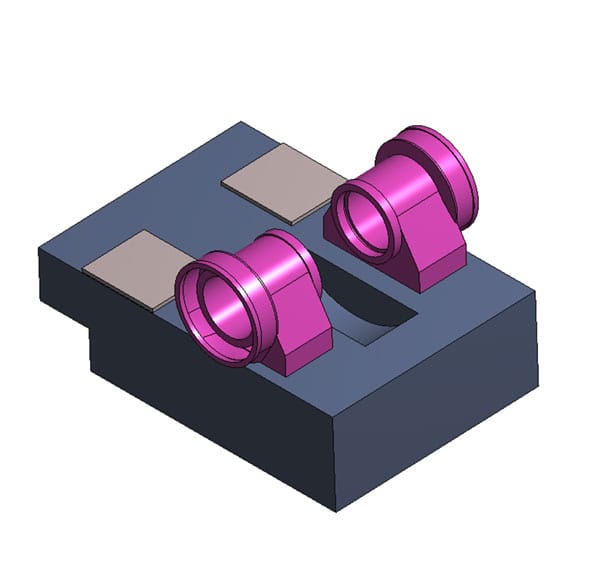
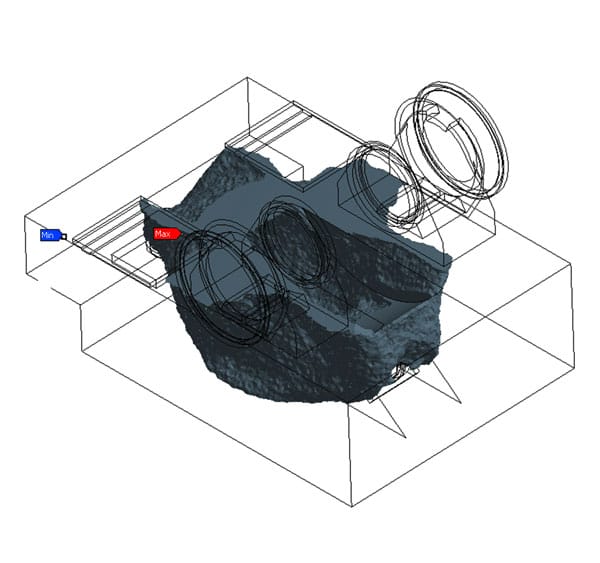
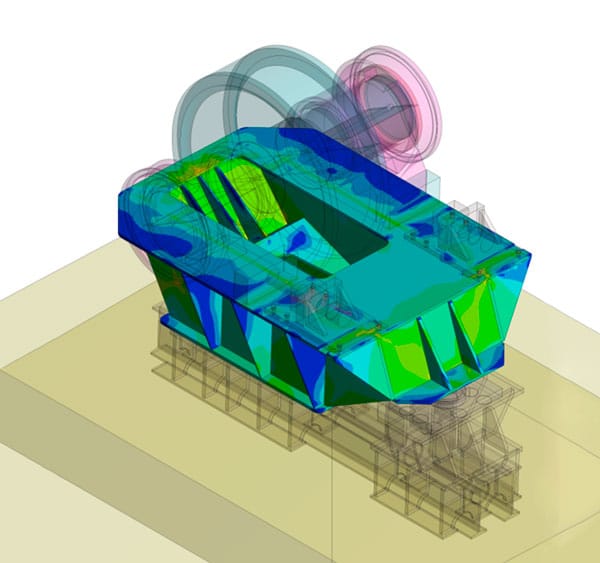
Der für diesen neuen Ansatz entwickelte modifizierte Workflow (siehe Diagramm unten) reduziert den Aufwand für die projektspezifische Dimensionierung und Optimierung. Kernelement dieses Engineering-Prozesses ist der konsequente Einsatz von hochautomatisierten 3D-Modellen, die durch die wichtigsten Variablen der Anlage gesteuert werden, wobei abhängige Größen und Konstruktionsdetails über programmierte Funktionen automatisch angepasst werden. Das jeweilige 3D-Modell bildet die Grundlage für die 2D-Fertigungszeichnungen, welche für die Produktions- und Berechnungsoptimierung notwendig sind, wobei jede Änderung des Basismodells automatisch zu Änderungen der Fertigungsdaten führt. Darüber hinaus reduziert eine konsistente Datenbank - ein 3D-Modell als Grundlage für alle Anwendungen (z. B. Erstellung von Fertigungszeichnungen) - Schnittstellenverluste.