thyssenkrupp has been a leader in many fields. How does the company stand out in the cement industry? What is the strategic positioning in the Chinese market?
We have a very long history in cement business. A key to maintain and develop the business for over one hundred years is that we always adapt to the changing demands of our customers. The cement industry is going to transform globally in three aspects I think. Firstly, cement production will become more efficient in terms of energy consumption and the utilization of resources; secondly, alternative fuels such as solid wastes will be used to replace coal and other conventional fuels; thirdly, and perhaps the most important is that, cement will be produced in an environment friendly way to reduce emission of dust, NOx and CO2. For this purpose, digital technologies will play also a very important role. Our mission is to provide innovative, reliable and sustainable solutions to help our customers deal with these challenges.
As the world’s largest cement market, China is currently facing the same issues. While customers focus on higher efficiency and productivity, environmental protection becomes much more important. To quickly respond to the local market and customer requirements, thyssenkrupp set up an experienced team for the Chinese market in 2018. And I’m honored to lead this team to provide advanced solutions and technical supports to our Chinese customers in the cement industry.
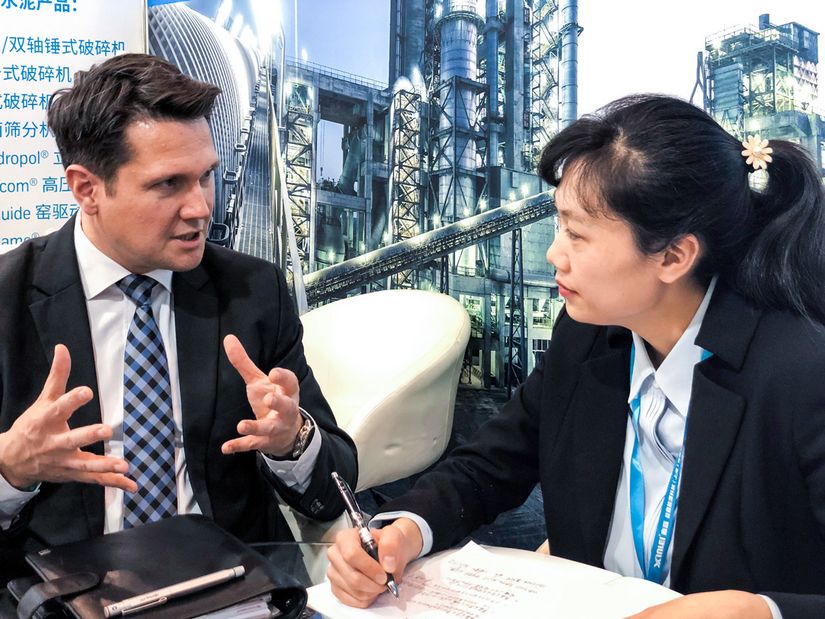
SCR has been one of the highlighted displays at the Cementtech 2019. What are the advantages of this technology and its current applications worldwide?
As we all know, environmental protection is on the top of China’s agenda. In 2019, some provinces and cities announced their latest emission standards for nitrogen oxides (NOx), which are even much stricter than European standards. At present, widely applied technologies in the Chinese market like selective non-catalytic reduction (SNCR) are unable to comply with the newly defined limits for NOx and NH3 emission. However, our SCR-technology (selective catalytic reduction) can meet the new standards and ensures a high conversion of over 90% NOx. Additionally, it can also significantly reduce the use of ammonia water. It is more economic and efficient.
We began to use this technology more than a decade ago in Europe, and we have implemented the most high-dust SCR cases in the world: so far a dozen SCR systems have been installed and put into operation worldwide. In 2018, thyssenkrupp received orders from Anhui Conch Cement Company Limited, one of the leading cement suppliers in China. For the first time, we introduced this well-verified technological innovation into China. In the near future, three sets of equipment will be put into operation in China, which will be an excellent example of SCR application in the Chinese and Southeast Asian markets.
Chinese and German customers might have different needs. So, we’ll provide the best tailor-made solutions to meet the individual requirements of our Chinese customers. Of course, one thing remains the same: we ensure excellent performance and high-quality of our equipment. This has always been our commitment to customers.
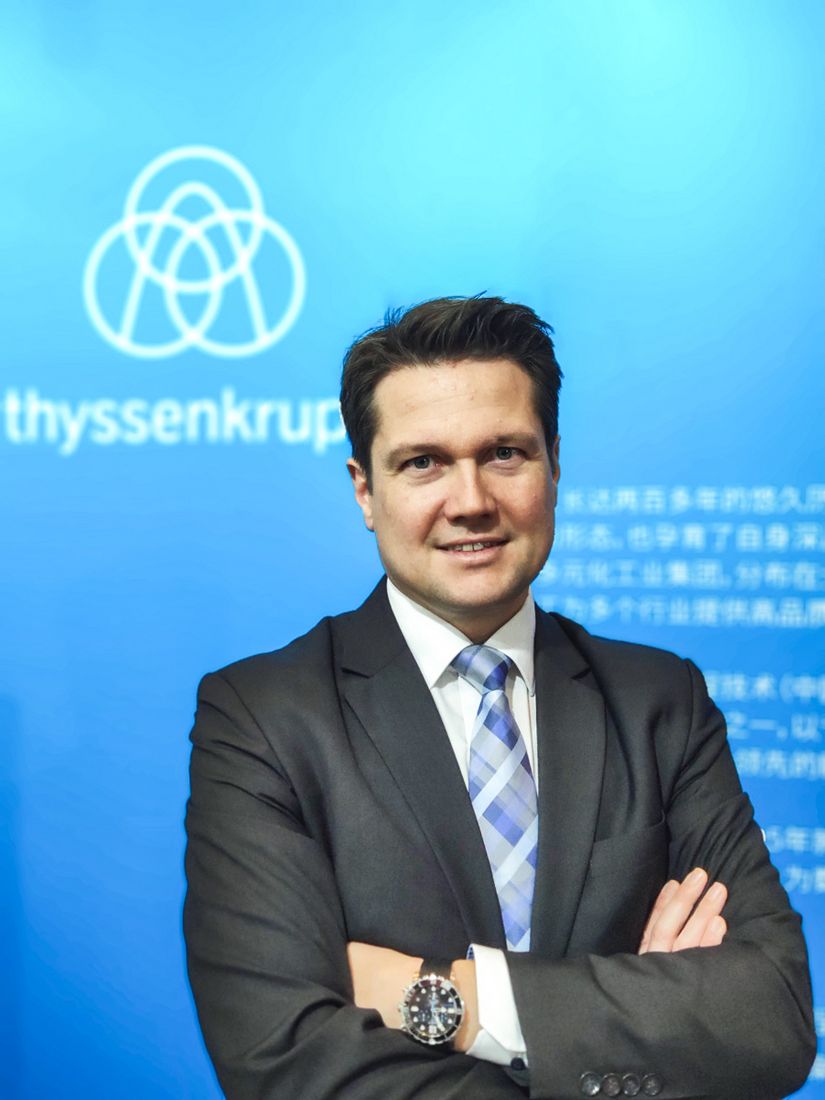
Head of thyssenkrupp’s Cement Business in China
What other innovative technologies does thyssenkrupp have in the cement industry and what’s your focus when doing business in China?
Saving energy and reducing emissions are the major tasks for China’s cement industry. Our focus in China is to provide our customers with reliable and environment friendly products and solutions for today and future. I just mentioned our SCR technology. Besides that we are currently introducing prepol® SC and polab® to China too. prepol® SC (step combustor technology) can significantly extend the burning time of solid wastes up to over 15 minutes at a very high temperature. It creates a new dimension of combustion, enabling the reuse of new solid wastes, and thereby saving fuel costs. At the same time, high efficiency, flexibility and easy maintenance make the system very reliable and effective. In 2013, we installed the first prepol® SC system in Germany. So far, more than 200,000 tons of solid wastes have been burned. In other words, it has saved more than 50,000 tons of coal, cutting down the customer’s cost significantly while protecting the environment.
So far, more than 200,000 tons of solid wastes have been burned. In other words, it has saved more than 50,000 tons of coal, cutting down the customer’s cost significantly while protecting the environment.
Dr. Björn Olaf Assmann,
Head of thyssenkrupp’s Cement
Business in China
The quality control system is a key drive in the modern cement production process. polab®, our laboratory automation system is a successful example. The fully automated quality control system includes sampling stations, pneumatic tube transport system and laboratory analysis equipment. It can reduce the consumption of raw material correctives, maintain high clinker quality and reduce the clinker factor in cement, and thus to make the complete production process more reliable and less energy and material consuming. Especially here in Asia we see a strong and clear trend towards fully automated systems. The polab® system allows a very high sampling frequency up to 6–8 samples per hour for optimal quality control. And to underline the attractiveness of polab® laboratory automation system: In most of our projects, with polab® customers can have their return on investment within 1–2 years.
Of course, we have many other advanced technologies and solutions, such as the polflame® VN burner with adjustable nozzles, which is an innovative technology designed for the cement industry. Compared with traditional multi-channel burners, the polflame® VN burner can achieve a quicker ignition even with low quality fuels. It can also realize higher fuel-air mixing by using fully adjustable nozzles. And the flexibility allows the customer to adapt the burner settings to various types of fuels, which can significantly save costs and achieve ecological benefits. We are expecting and also very confident that our well verified innovative technologies will help Chinese customers achieve greener, more economic and efficient cement production today and tomorrow.