Cement plant engineering is a challenging and highly demanding process. This is mainly due to four restraining parameters: the small quantities built; the very large dimensions of the equipment; the need for extremely high plant availability; and requirements that change from order to order (e.g. plant size, scope of delivery, process engineering, logistics concept, etc.). As a result, many if not most projects are unique from an engineering point of view.
3D model of a cooler housing, to reduce the automation complexity the overall design was split into separate modules
This new approach enables solutions tailored to our customers’ wishes – without drastically increasing our engineering workload. And our high product quality is enhanced even further.
Dr. Justin Bisping
Head of Design and Engineering Pyroprocessing Technologies,
Cement Business Unit, thyssenkrupp Industrial Solutions
Besides the usually one-off set of parameters, engineering projects are subject to the generally applicable demand for fast and cost-effective solutions based on high-quality and safe products. Over the past decades, these challenges have led to a build-up of expertise among reputable vendors and the use of the finite element method (FEM) for computational optimization. Up to now, however, this approach has been typically limited to individual project development or product maintenance, while on-the-fly integration into a running project was seldom possible due to limited processing or programming capacities.
These difficulties were the starting point and motivating factor for a new approach developed by specialists from the Cement Technology Business Unit at thyssenkrupp Industrial Solutions and based on state-of-the-art engineering tools – 3D CAD in combination with FEM – and highly automated standard tasks, e.g. creation of manufacturing drawings. As a result, on-the-fly optimizations and order-specific adjustments can now be carried out in the course of a running contract.
Exemplary computational optimization of a base plate of a rotary kiln. Topology optimization was used as a starting point to optimize weight and manufacturability.
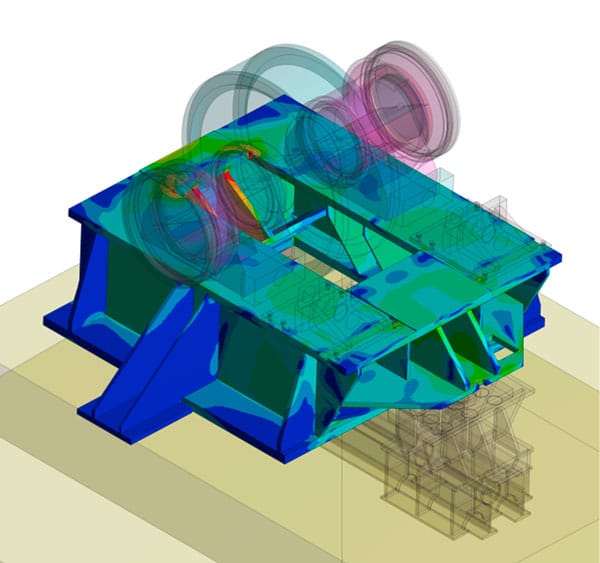
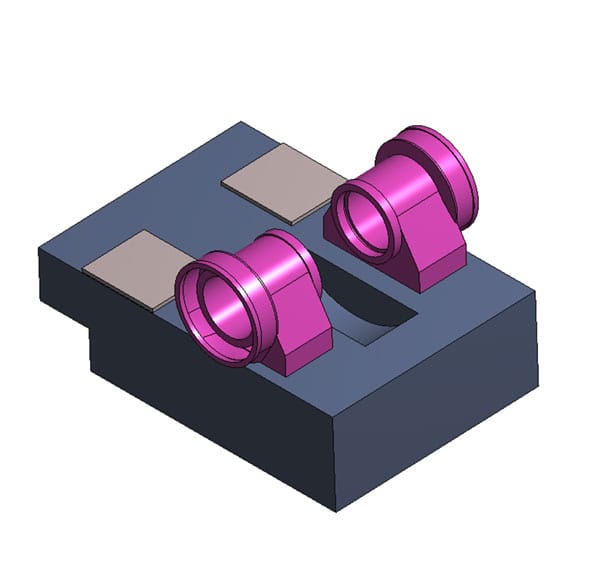
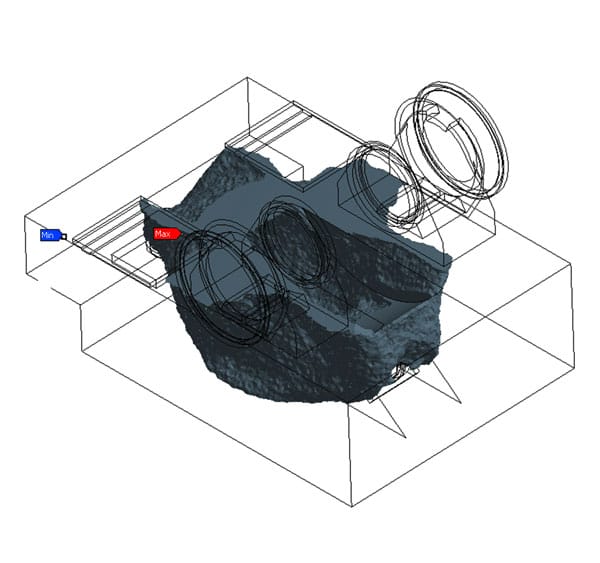
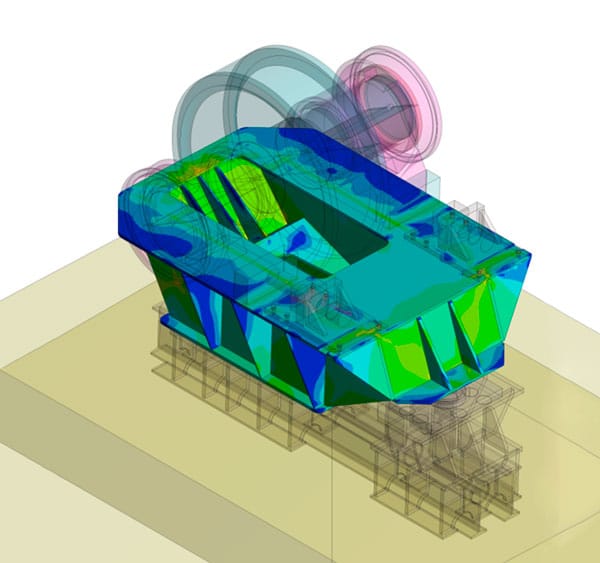
The modified workflow developed for this new approach (see diagram below) reduces the effort required for project-specific dimensioning and optimization. The core element of this engineering process is the consistent use of highly automated 3D models controlled by the key characteristics variables of the equipment, with dependent sizes and design details being automatically adapted via programmed functions. The respective 3D model forms the basis for the 2D manufacturing drawings required for production and computational optimization, with any change in the basic model automatically leading to changes in the manufacturing data. Moreover, a consistent database – one 3D model as the basis for all applications (e.g. creation of production drawings) – reduces interface losses.