Social and political pressure is growing
“Cement production is not only one of the most energy-intensive processes in the world, it is also responsible for around seven percent of global CO2 emissions,” explains Dr. Georg Locher, Head of Technology, Innovation & Sustainability at the Cement Technologies business unit. “By 2030, annual cement production will increase to over 4.8 billion tons. Social and political pressure is increasing, not only in Europe. Just look at the current debate over CO2 and NOx limits. The topic has also reached countries such as China, where much tougher NOx emissions standards were introduced only recently.”
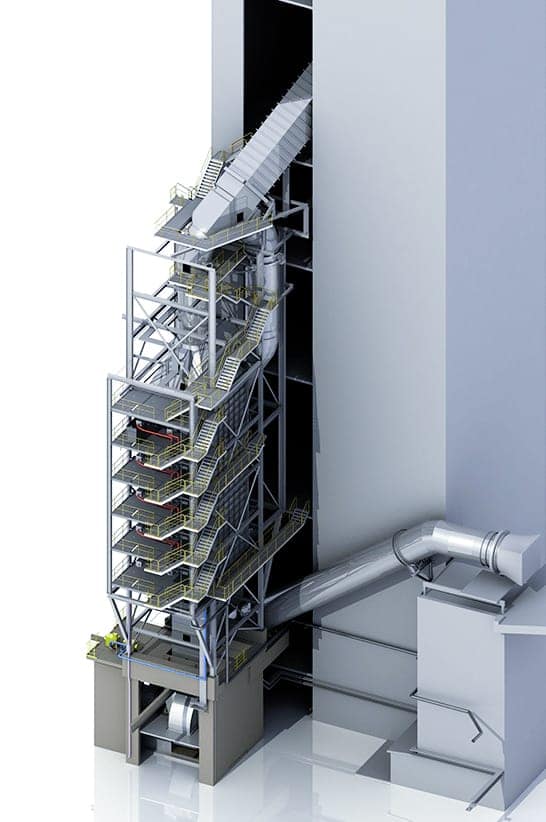
Industry is showing great interest in sustainable products
This year's “Global Future CEM Exhibition & Conference” in Brussels, an important meeting place for the cement industry, was also held under the motto of “CO2”. Addressing more than 100 industry experts, Dr. Luc Rudowski, Head of Product Management, Technology, Innovation & Sustainability, presented thyssenkrupp’s first four market-ready solutions on the path to the green cement plant – solutions that attracted a lot of attention.
“We asked ourselves what the cement plant of the future will look like,” reports Rudowski. “We see great potential in reducing emissions, in new binding agents, in optimizing resources and energy, and in digitization along the entire process chain. We have already launched four solutions that increase the competitiveness of the cement industry: polysius® NOx reduction, polysius® carbon neutrality, polysius® fuel substitution and polysius® activated clay.”
We asked ourselves what the cement plant of the future will look like. We see great potential in reducing emissions, in new binding agents, in optimizing resources and energy, and in digitization along the entire process chain.
Dr. Luc Rudowski
Head of Product Management,
Technology, Innovation & Sustainability
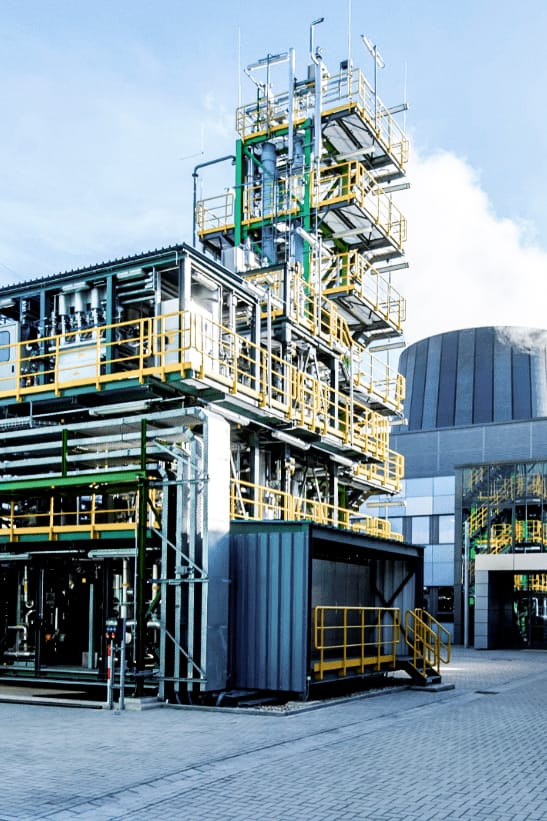
Cleaner air thanks to CemCat
NOx reduction means complying with emissions standards and protecting the environment and wildlife. In more and more countries, reduced NOx and NH3 emissions are required by law. Plants that fail to comply with the limits are shut down. Plant operators who reduce NOx and NH3 emissions are acting in an environmentally responsible way. They have to meet the expectations of politicians, society and the local community. Our CemCat SCR solution aims to improve air quality through flue gas treatment and process optimization measures.
Capture CO2 where it is produced
Excessive emissions of CO2 in the cement industry are exacerbating climate change. Today’s CO2 emissions from cement plants account for seven percent of global CO2 emissions. The implementation of the Oxyfuel process could take cement plants a big step further towards achieving long-term carbon neutrality. thyssenkrupp is also working in other sectors, such as steel production with Carbon2Chem®, to isolate and reuse CO2. Both technologies use synergies from the chemical and renewable energy sectors and show that the capture, storage and utilization of CO2 to achieve carbon neutrality is not a contradiction in terms.
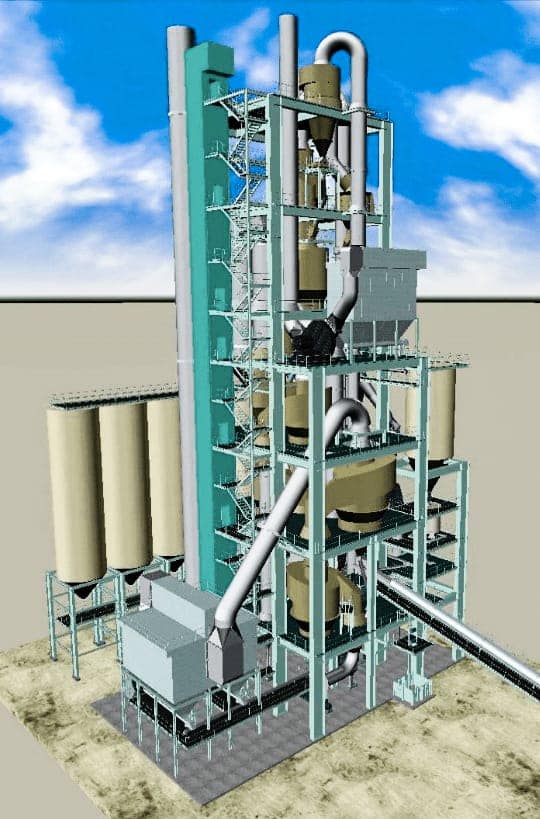
Alternative fuels are gaining importance
How do I avoid the use of oil, gas or coal and instead convert waste and biomass into heat? With polysius® fuel substitution, a cement plant can be operated with up to 100% alternative fuels. Used in the precalciner and rotary kiln, they replace natural resources and thus reduce CO2 emissions from fossil fuels. With polysius® fuel substitution, thyssenkrupp enables plant operators to easily implement the entire waste-to-energy chain from a single source while meeting all emissions standards. At the same time, a substitution rate of up to 100% means independence from scarce natural resources.
Clinker substitutes save resources
By using more clay in their plants and reducing the clinker content to 50 percent, our customers save money and emit less CO2. The use of activated clay instead of clinker has a threefold impact on the cost and sustainability of cement production. First, less clinker means less CO2 emissions. Second, clay reduces energy requirements by up to 40 percent – because activation takes place at temperatures below 900 degrees Celsius instead of 1,450 degrees Celsius. This significantly reduces energy costs, especially when renewable energy and fuel sources are used. Third, replacement makes the cement more climate-neutral and improves its quality.
Sustainable solutions for the cement plant of the future
“The global trend towards urbanization and the associated expansion of infrastructure is increasingly coming into conflict with the issue of sustainability and posing unresolved questions for the industry,” says Pablo Hofelich, CEO of the Cement Technologies business unit. “Together with our long-standing customers we are therefore developing appropriate solutions and products, taking the next step in cement plant construction. Our answer is sustainable, green, automated and part of an increasingly digital value chain”.